R&D Story 02
Supporting global automotive innovation with adhesive technology
Sunstar Engineering conducts R&D at its different sites around the world so as to support all production processes in the fast-changing automobile manufacturing industry.
Adhesives are an indispensable part of automobile manufacturing
Sunstar Engineering has long focused on the development of adhesives, sealants and coating materials used in building and automobile manufacturing. The adhesive line for automobiles was launched in 1964 with the development of Penguin Cement 332. Since then, we have constantly invested on research and development, becoming one of the few manufacturers capable of producing adhesives and sealing materials applicable to every process of automobile manufacturing. In recent years, we have put special emphasis on the development of weld bond adhesives.
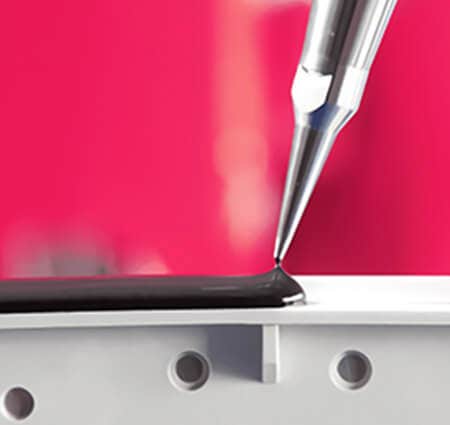
Worldwide automobile sales have been increasing for seven consecutive years since 2010, with over 90 million cars sold in 2016 alone. In this massive global market, technological development is underway to reduce environmentally hazardous substances and improve fuel efficiency, as car manufacturers innovate body designs to reduce weight. Today, cars are made of various lightweight materials such as aluminum, magnesium, and organic compound composites instead of steel. Amid this material diversification, in an effort to reduce weight, automotive adhesives play an important role.
Proprietary ingredients enable high adhesion and durability, allowing weight reduction in automobiles
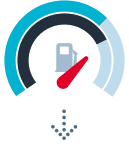
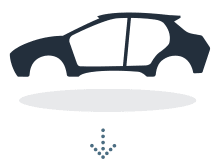
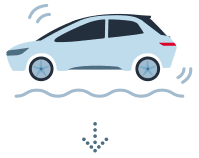
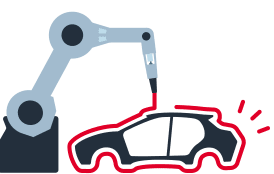
In order to improve fuel efficiency, vehicle weight has to be reduced and, to obtain that, thinner steel sheets are used in the body.
However, as these sheets become thinner though, the body’s rigidity (its ability to resist bending and torsion) is also reduced.
Weld bond adhesive is used in the weld bond process, which combines spot welding and adhesives together to ensure the vehicle body’s rigidity and strength.
The weld bond adhesive strengthens the single point joints made by spot welding, transforming them into a surface joint. By dissipating the stress accumulation in the welded area, the adhesive enhances the overall durability and rigidity.
This contributes to weight reduction by allowing the use of thinner steel sheets and reducing the number of necessary parts.
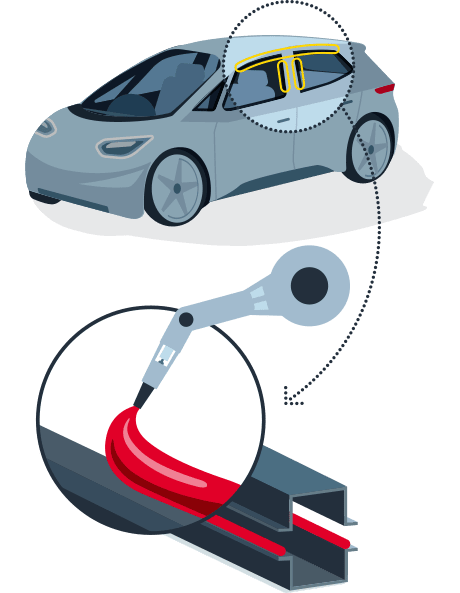
Epoxy resin is the main component of weld bond adhesive, that’s responsible for giving it a high adhesive property and rigidity. Although hemming adhesives which are used for joining of door panels are also epoxy-based, the requirements for durability against vibration and distortion are higher for weld bond adhesives.
Sunstar Engineering’s weld bond adhesive achieves its high durability by blending components modified with special rubber, adding extra strength.
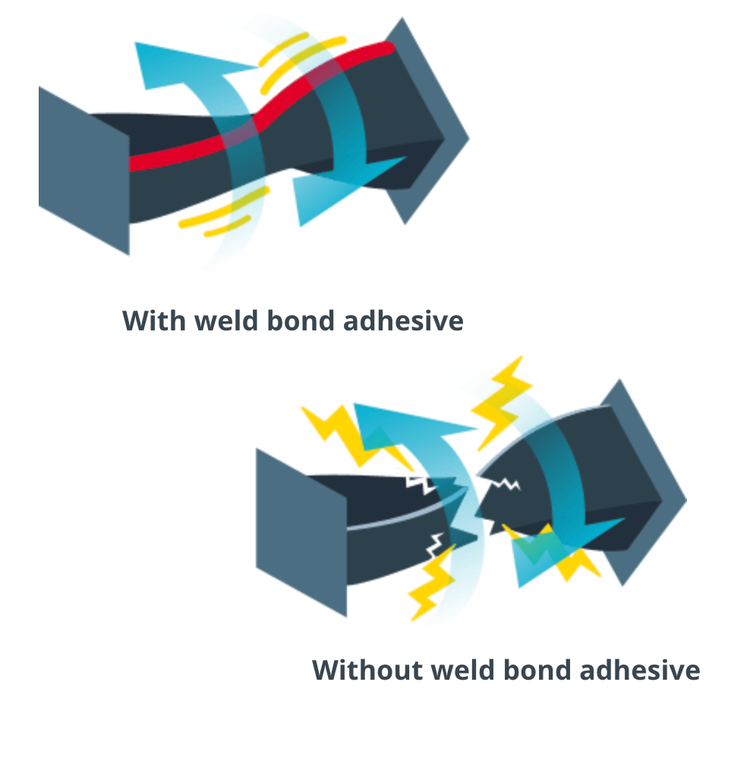
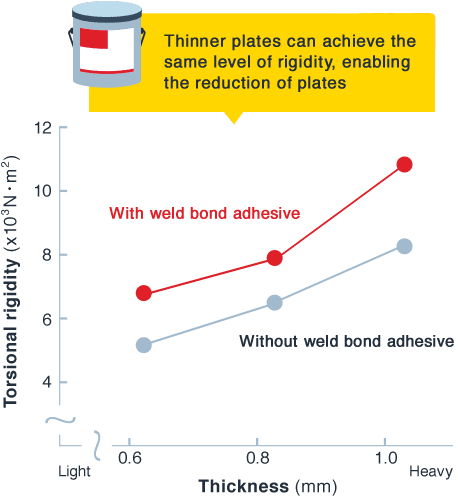
One of the few manufacturers producing every type of automobile adhesive
Developing numerous products for each step of the manufacturing process, at or above industry-standards for quality assurance
Sub-standard adhesives endanger the lives of people driving a finished car at risk. For this reason, researchers at Sunstar Engineering conduct risk prediction tests, using test parameters based on past experiences. For example, the Storage Stability test evaluates adhesive properties and performance to ensure quality does not change after long-term storage. The tests have been repeatedly revised and refined to prevent problems even when vehicles are used in unexpected ways.
One of the few manufacturers producing every type of automobile adhesive
Developing numerous products for each step of the manufacturing process, at or above industry-standards for quality assurance
Sub-standard adhesives endanger the lives of people driving a finished car at risk. For this reason, researchers at Sunstar Engineering conduct risk prediction tests, using test parameters based on past experiences. For example, the Storage Stability test evaluates adhesive properties and performance to ensure quality does not change after long-term storage. The tests have been repeatedly revised and refined to prevent problems even when vehicles are used in unexpected ways.
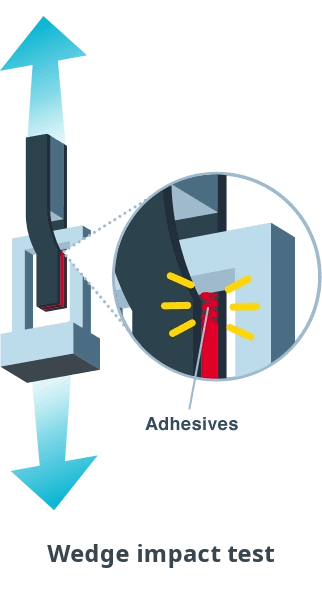
The weld bond adhesive is designed to be used during automobile production. For example, while the weld bond adhesive holds steel plates for welding, it should not hinder the welding in the subsequent car body assembly line. The adhesive should not run out or deform under water pressure during either hot water washing or painting.
In addition, the adhesives require curing during the electrodeposition coating (namely the electrodeposition of a coating film of paint or resin on the metal surface), and in recent years the need to cure at lower temperatures in a short period of time is increasing. Sunstar Engineering developed a weld bond adhesive that not only adapts to automobile manufacturing processes, but also contributes to energy saving by lowering the curing temperature and shortening the heating time thanks to its low-temperature, fast-curing technology.
Automobile Production Line
Global R&D cooperation to expand overseas markets
With the unique advantage of handling adhesives for all automobile manufacturing processes, Sunstar Engineering is a leader in research and development.